Surface treatment of self-tapping screws: Most self-tapping screws are coated with galvanized or zinc phosphate. Cadmium plating is rarely used because of its high cost and toxicity. If appearance is important, nickel or chromium plating can be selected.
1. Appearance treatment will not only increase the scale (such as the reduction of holes, etc.), and different appearance treatments will affect the relationship between torque, tightening degree, and strength. Therefore, when doing penetration experiments, it must be based on zinc plating and cadmium plating. Or phosphate disposal has different rules. When testing the applicable tapping hole diameter, the screws used must be screws with the same appearance.
2. High-hardness, small-scale self-tapping screws often fail in use due to hydrogen embrittlement. Self-tapping screws have to be carburized in order to penetrate into the iron plate. High hardness and high carbon content will occur after carburizing treatment, and hydrogen embrittlement will occur during electroplating or pickling treatment in this case.
Hydrogen embrittlement test: The hydrogen embrittlement test is mainly to test whether the self-tapping screw has residual hydrogen in the screw arrangement and whether it will embrittle the self-tapping screw. (Generally, the embrittlement does not occur in a while, and it must be given (The stress will only show up) The electroplated or coated screws should be installed in the test iron plate and steel flat washer as specified in Table 3. Type (Oval) screws use a matching chamfered distance steel sheet. The thickness of the flat washer or distance piece installed on the lower bearing surface of the head should be able to fit the maximum invalid tooth length of the screw.
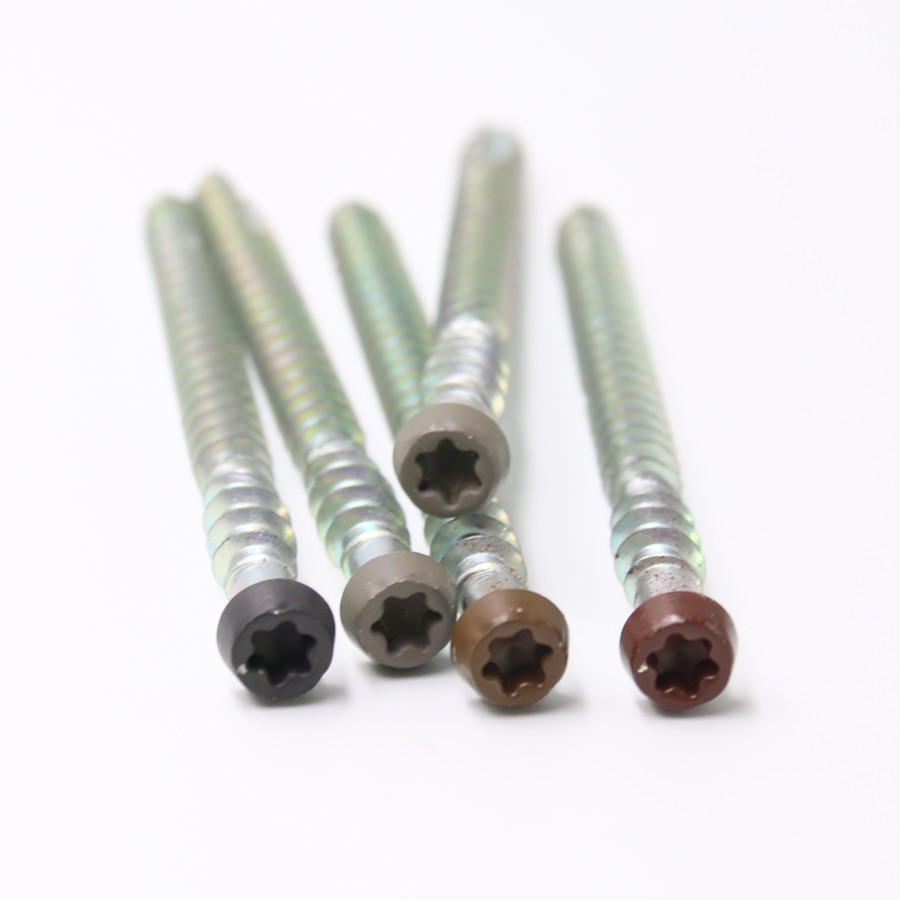
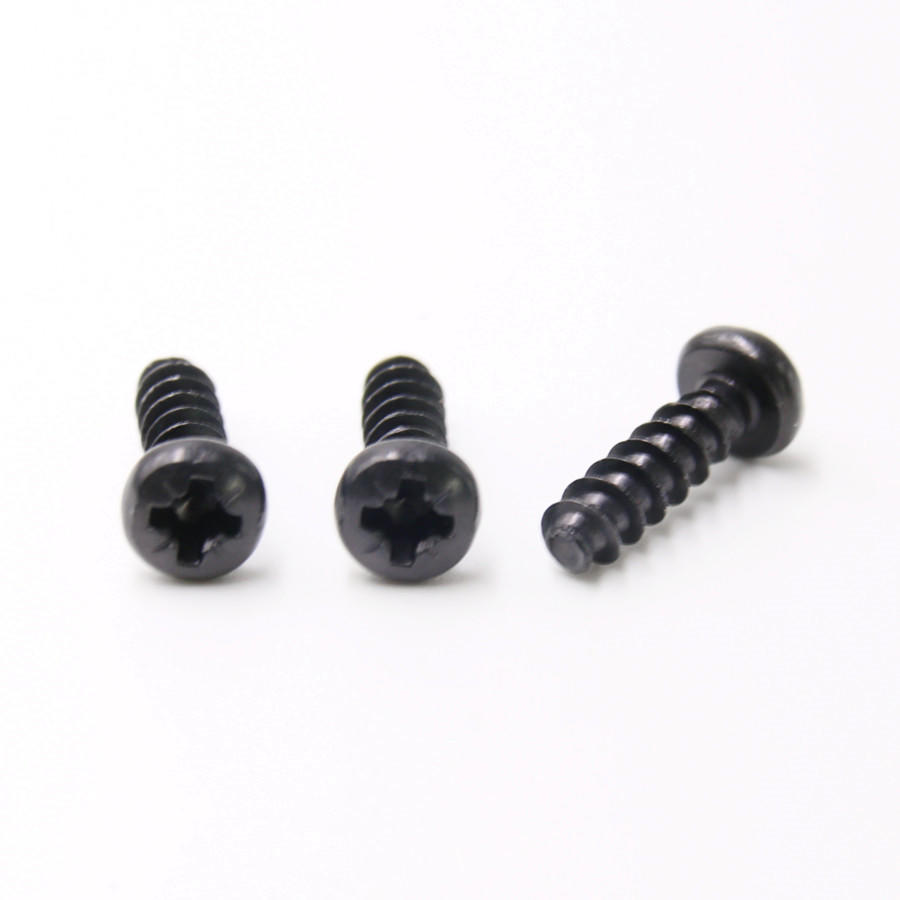
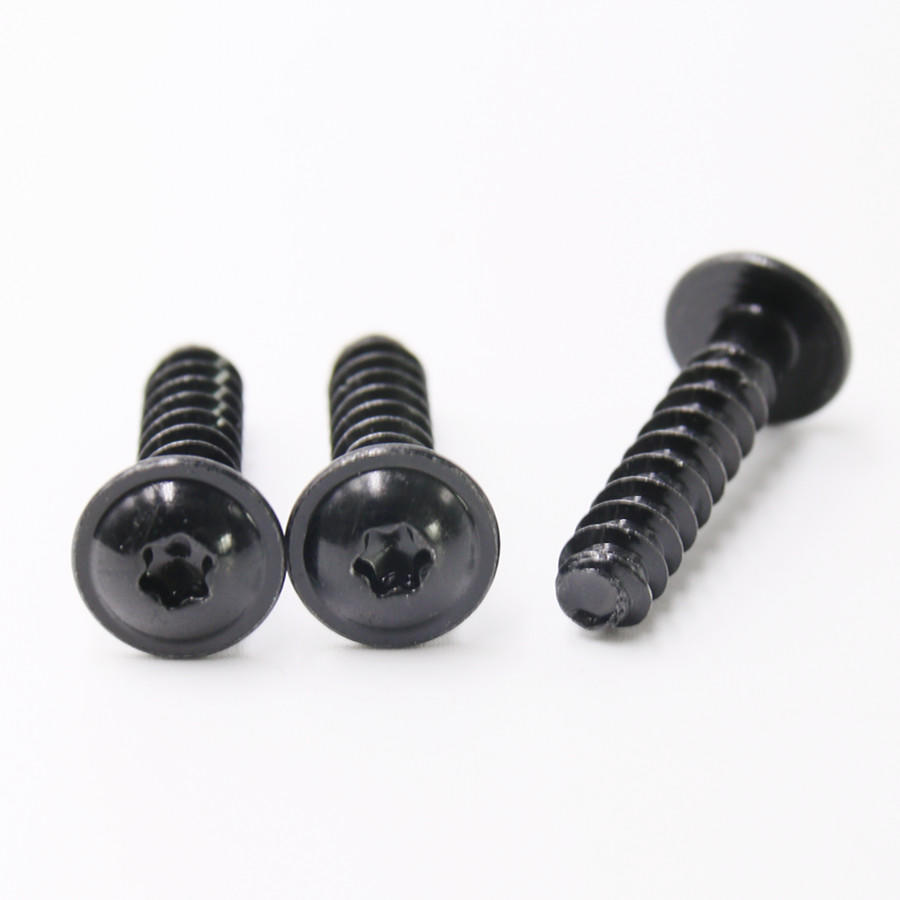